Previously, we wrote a blog about one of the more common topics that we discuss with our clients – the importance of warming up a spindle properly. Today, we’re covering a related and equally important subject — the importance of properly winding down your machine tool spindles when work is done.
When and Why Does a Spindle Need to be Wound Down?
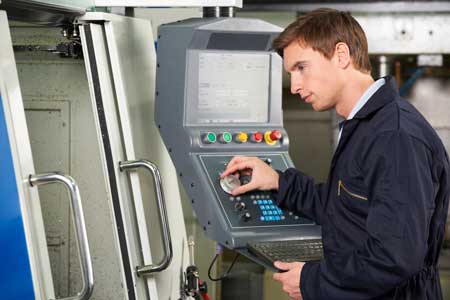
In the same way that we recommend a spindle be warmed up after any period of idleness, we recommend that you wind your spindle down correctly after every period of use. Whether it’s for a period of extended maintenance, a week or holiday, or just change-of-shift, if you’re shutting down you should wind down the spindle properly.
There are multiple reasons why we are enthusiastic about proper wind down procedures. For example, doing so helps improve a spindle’s health. But the primary reason is to avoid damage and contamination by manufacturing process debris. If a spindle is allowed to cool too quickly, while there are contaminants on the external spindle surfaces, you run the risk of that process debris ingress into your spindle by the process of capillary action like solder into a joint.
How to Wind Down Your Spindle
There are hundreds of spindle manufacturers, and many more spindle models, each of which has unique processes and requirements for winding down. For that reason, we recommend that you always follow OEM instructions. However, there are a few general rules for spindle wind down that should apply to just about any model:
- Reduce spindle speed gradually – run at 50% power for 5 to 10 minutes, and then at 25% power for 5 to 10 more. This helps to control the cooling process, easing the spindle into it.
- During wind down, it’s critical to maintain positive air pressure (air purge) on the machine until the spindle has completely cooled to ambient temperature.
- Periodically wipe down spindle surfaces during wind down, using a soft, clean cloth to keep the spindle both clean and dry. This prevents manufacturing process debris from being drawn into the spindle assembly as mentioned earlier.*
- Clean any coolant residue from the entire work area, including the spindle.
- Ensure that all systems are powered off properly. This includes the coolant system if it’s powered separately.
*Important note: Do not ever use air guns to clean the spindle assembly, especially the face and shaft ID. It may seem like a quicker, lower-touch alternative to using a cloth, but the fact is that you can do serious damage. The pressure of an air gun can easily overpower the positive air pressure (aka air purge) of the spindle, forcing air, contaminated coolant, and machining debris into the critical internal spindle components, such as bearings and others. Using an air gun, you are not blowing debris, chips and coolant off, you are blowing it in.
During and immediately after wind down is also an ideal time to conduct inspections and checks. A few important ones that we recommend performing include:
Inspect and clean toolholders daily, not just during wind down. If tapers have fretting, chip marks or rust, replace them.
- Oil level in the lubricator
- Condition of the tools
- Drawbar retention force using a force gage
- Verify that the coolant system is functioning properly
- Visual inspection of spindle for any signs of wear, damage, or abnormalities
- Listen for any unusual noises
- Documentation – record any observations, issues, or maintenance performed.
What Happens if I Don’t Do It?
If you rush through a wind down, you might get lucky and experience no ill effects for a while. But you risk — or, if you skip the process regularly, you practically guarantee — the buildup of swarf on the spindle surfaces and possible ingress into the spindle assembly. This can lead to diminished performance and bearing life, as well as excessive heat, vibration and finished parts that are out of spec or otherwise of reduced quality. Longer term, you’re looking at inevitable spindle failure which can be costly and cause loss of production.
Our conclusion about the importance of spindle wind down is the same as it was for spindle warmup: it takes a few extra minutes to perform the steps properly, but this a small price to pay when compared to the alternative.