Machine tool monitoring has become an indispensable asset to machine shops operating in today’s competitive manufacturing landscape. Reactive maintenance strategies are no longer sufficient in an environment where customers will not tolerate unexpected machine tool failures that impact production schedules, delivery dates, and part quality. Implementing monitoring-based predictive maintenance practices allows manufacturers to solve problems early and gain a proactive edge, ensuring efficient operations, happier customers, and cost savings.
A successful up-time strategy boils down to three actions: detect, analyze, and correct. Let’s review each:
Detect
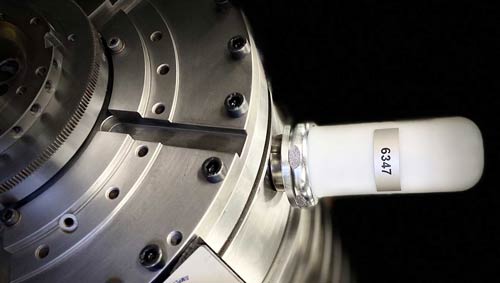
Early detection of equipment issues is the goal for all machine tool monitoring programs. This allows maintenance teams to plan for repairs or changeouts during planned outages to minimize unexpected disruptions. Key technologies for monitoring machine health include vibration analysis and acoustic emission (ultrasound) monitoring. Vibration helps identify problems like imbalance, misalignment, and looseness before they escalate into critical failures. Ultrasound, on the other hand, excels at detecting early-stage bearing faults, often even before vibration anomalies appear. Remember, as we’ve discussed in the past, these earlier issues aren’t audible to the human ear. Therefore, having ultrasonic sensors “listening” becomes crucial.
Vibration and ultrasound technologies work together to help technicians understand what actions may be taken to correct the problem early. They can also predict how much time is left until scheduled maintenance must be planned. Through data trending, an important part of machine tool monitoring, both vibration and ultrasound measurements are watched over time to assess machine health and predict potential issues. This involves comparing collected data to established baseline levels and industry standards like ISO 10816 for vibration alert and alarm levels. Exceeding these thresholds signifies that there are potential problems that require investigation.
Ultrasound is measured in decibels (dB). Ultrasound standards developed by NASA can also be compared to the ultrasound trend. For instance, when compared to the collected baseline, an increase of 8 dB indicates that a machine tool’s bearing is under-lubricated. Lubricating the bearing will lower the ultrasound level back to an acceptable level and a new baseline can be established. An increase of 12 dB means that the bearing has moved into late-stage bearing failure.
Analyze
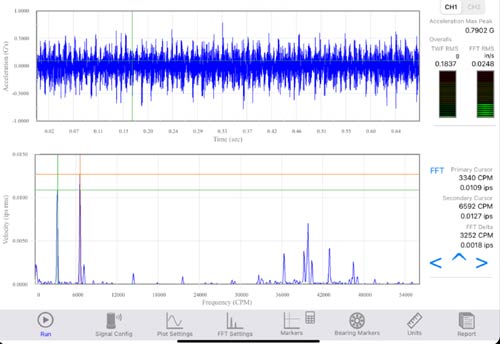
Trends are monitored until an alert or alarm sounds. Once the readings exceed acceptable vibration levels, it’s time to analyze the data. This is done by trained analysts, online analysis tools, or remote third-party professionals.
Once an issue arises, its cause must be determined. Analysis can indicate how to mitigate the problem so it can be caught early. Faults like imbalance, misalignment, and looseness cause the majority of machine tool problems, leading to bearing failure, and early intervention can prevent complete failure.
A complete Failure Mode and Effects Analysis (FMEA) should be performed to determine the root cause to eliminate and prevent this fault from occurring in the future.
Correct
Detection and analysis are a big part of any machine tool monitoring program, but correction is where the rubber meets the road. Determining when to intervene can be difficult. Here are some questions to ask:
- Can or should production be interrupted to perform the repairs?
- What is the cost of repair and downtime if we run it to failure?
- When is our next maintenance outage and will it last that long?
Once a fault is found, it needs to be documented. Repair planning and scheduling need to happen. Parts and the proper tools need to be part of the planning and scheduling process, as well as the scheduling of the technicians and millwrights with the training and knowledge to do it right the first time.
Machine Tool Monitoring – It’s Time
Detecting, analyzing, and correcting problems early with machine tool monitoring can reduce maintenance costs by as much as 50% and increase uptime by as much as 30%. Proper training in the use and application of predictive maintenance tools is essential to your success.
Predictive maintenance solutions are becoming less expensive, simpler to use, and readily available. Is this your year to start a machine tool monitoring program?
> Click here to learn more about our industry-leading machine tool monitoring solutions