The heart of any good predictive maintenance program is a robust machine monitoring system. The world of monitoring systems is as vast as the equipment types in use today. They differ in form and function based on machinery type, metrics being monitored, industry, and more. Today, we focus on on the machine monitoring systems and software suitable for use in spindle/machine tool applications.
The Importance of Machine Monitoring Systems
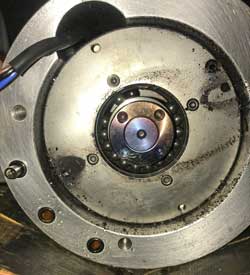
Boiled down to their core, predictive maintenance programs utilizing machine monitoring systems are important for one primary reason — cost savings.
As we’ve discussed in the past, it’s a relatively common practice to run spindles to the point of failure. The problem is that, though there are some small cost savings in the short term, the costs in the longer term can be significantly higher.
Spindle repairs at the point of failure are typically three or more times more expensive than repairs at the first sign of an issue. And the costs don’t stop there: unplanned downtime is quite a bit more expensive than planned maintenance downtime. Monitoring your machine tools helps you identify issues early, when they’re easier and less expensive to fix.
Machine Monitoring Systems Components and Functions
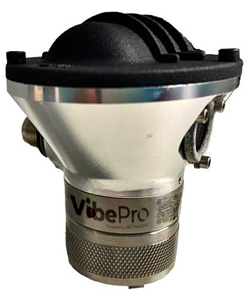
Though monitoring systems vary in complexity, they’re focused around two primary components: sensors and machine monitoring software.
Sensors are typically some form of accelerometer. Either permanently affixed to a machine tool or portable, sensors measure a variety of metrics, including:
- Vibration
- Sound/Ultrasound
- Temperature/Thermography
- And more
The Role of Machine Monitoring Software
On their own, no matter how powerful or sensitive they are, sensors will not do you very much good. Machine monitoring software is needed to process and generate reports of the collected data. The software is often an app, like the VibePro 10 iPad app.
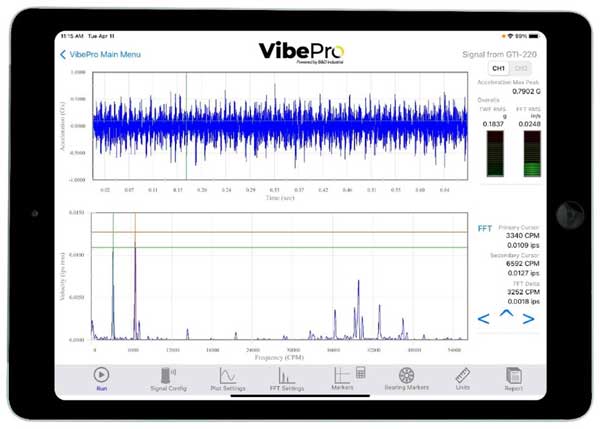
Machine monitoring software takes the raw data from sensors and converts it to a human-understandable form. The software displays the data visually so we can read it, track changes over time, compile both periodic and event reports, sound alarms when key metrics are outside of predefined range, and more.
Machine monitoring systems are powerful tools with many benefits over traditional predictive maintenance methods. They allow for real time machine health data collection, which is presented graphically through robust user-centric dashboards. This critical data allows for improved forecasting accuracy and strategically planned downtime. Their real time alerts and notifications allow operators to resolve issues early, before they grow into much larger headaches. Though machine monitoring systems require some investment upfront, they can pay for themselves quickly thanks to all of the cost-saving advantages they provide.
Want to see if a machine monitoring system can help improve your bottom line?
Click here to learn more about our spindle analysis tools or to reach out to us to address your questions and specific needs.