One topic we hear more and more about these days is reliability. Essentially, this refers to initiatives designed to keep manufacturing facilities up and running efficiently and, well, reliably. It consists of several components such as predictive maintenance, planning, scheduling, data collection and analysis, and much more. Today, we’ll review a critical component to the success of any machine shop’s overall reliability program, regardless of size or industry.
Let’s imagine this scenario: your driveway has nails on it from that handywork you did over the weekend. When you pull your car out of the garage on Monday morning, you’re likely going to get a flat tire. You’ll go to the mechanic to have it fixed and when you return home, you will identify the cause of your tire failure — the aforementioned nails — and clean them up so that you do not get another flat tire when you pull your car back in.
This will no doubt seem incredibly obvious: remove the cause of the failure in order to prevent it from recurring. Yet for some reason, in industrial spaces and particularly with machine tool spindles, companies seek out repair services and rarely attempt to learn or address what caused the failure in the first place.
Boost Profitability with Root Cause of Failure Analysis
You can probably see the issue with this mode of thought. You’re already experiencing unplanned downtime, and you want to just get the repair done and get the machine back in service. But without addressing what caused the need for the repair, you’ll eventually need to make the same repair again. And again. And again.
Before you know it, you’ve spent untold thousands of dollars on repairs that could have been avoided. Depending on how extensive the required repairs are and how often they recur, you can be taking a good hit to your profitability.
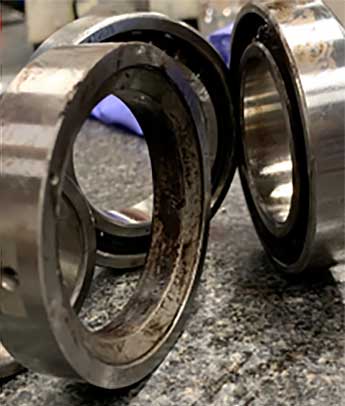
Luckily, the solution is simple. Every time you have a spindle failure that results in repairs, don’t settle on just the repairs — a Root Cause of Failure Analysis should be done. A Root Cause of Failure Analysis is exactly what it sounds like: figure out what caused the spindle failure, and remedy the issue. For instance, when we take in a spindle for repair at GTI, one of the first things we will do is a failure analysis. We provide customers with a detailed report on not just wait cause the failure but what most likely caused the cause-of-failure. If needed, we can also send a specialist to your facility to assist in determining the root cause. They will investigate and identify other issues beyond the spindle itself, such as the machine it’s in, the environment the machine operating under, related system components, and so on. For instance, improper lubrication is often a contributing cause to spindle failure.
5 Common Causes of Spindle Failure
In the course of our spindle repair work, we’ve encountered any number of failure causes, from the mundane to some more unexpected ones. However, out of the countless repairs we’ve undertaken over the years, we’ve found that the majority of failures are caused by one of five things:
-
The rear of the same spindle had ample, clean oil and no contamination evident, allowing us to rule out lack of lubrication or contaminated oil supply as the root cause of failure. Improper lubrication — Maybe it works for bike chains, but with machine tool spindles, more grease is not always better. Machinery, and particularly spindles, have very specific lubrication requirements. Straying from prescribed specifications — whether using too much, too little, or a different type — can quickly lead to spindle failure.
- Contaminated lubrication — This one speaks for itself. Lubrication is meant to help different parts move together with a minimum amount of friction. If your lubrication is contaminated with anything, from as small as dust to as large as metal shavings, this will prevent the lubricant from properly doing its job.
- Unbalanced tooling — It pays to take the extra time to get your tool holders/tooling set up properly, within tolerances and ISO balance grade specification. If your tool holders/tools are not within specification and/or out of geometry by even just small amounts, you’re inviting spindle failure (not to mention quality issues for the components you’re machining).
- Electrical mis-programming — Giving too much or too little power to your machinery is a lot like unbalanced tooling in that you only need to go out of specifications by miniscule amounts before your machinery begins to be negatively impacted.
- Operator/machine crashes — Human error will always be a factor, and there’s not much you can do to prevent it. Simply train your operators as thoroughly as possible, and retrain them regularly. For the machine, make sure to keep good maintenance practices (including software updates). Because failures caused by crashes tend to be the most serious.
Addressing the root cause of failure is as important as getting the spindle properly repaired quickly and back in service. Sometimes the fix is simple (like adjusting your lubrication levels). Occasionally the solution requires something more extensive, like outright redesigning and rebuilding older equipment. Whatever the case, with a root cause of failure analysis and taking corrective action, you’ll help keep repair bills in check, and have a much successful and efficient reliability program.