Like all moving machine elements, bearings in spindles can fail due to a variety of causes. While normal wear and tear is one of these causes, there are specific points of failure that are more common than others. Before it becomes necessary to repair a spindle due to bearing damage, consider these factors that may lead to spindle bearing failure:
Improper Lubrication:
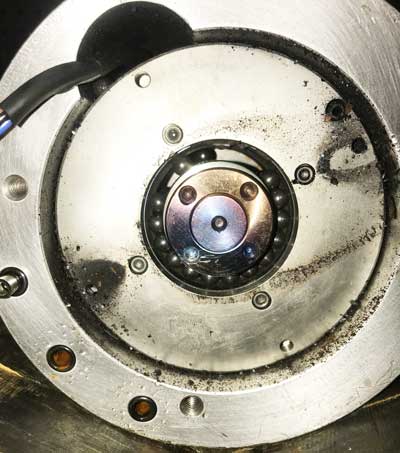
Lubricant is critical when it comes to spindle performance; it affects maximum operating speed, temperature and vibration levels. Improper lubrication can cause bearing failure in several different ways. The most prevalent lubrication error is using an insufficient amount. This can lead to increased wear due to friction as well as thermal damage due to higher operating temperatures. The resulting damage to bearings can include rolling element deterioration, raceway deterioration, cage fragmentation, and eventually spindle failure.
When it comes to lubrication, here are three things to keep in mind to ensure longer bearing life:
Always use the right type of lubricant: There are many types of bearing lubricant – be sure that you are using the right compatibility and viscosity. Quality is also a significant factor, and a sub-par lubricant can increase the chance of wear in a bearing.
Always use the right amount: An insufficient amount of lubrication can cause damage to your bearings, but too much lubrication can also cause issues. Following lubricant specifications for your machinery will increase the life-span of your bearings.
Always apply lubrication at the right time: Applying lubricant too often or not often enough can lead to bearing failure, even if you are using the right type and amount. Adhering to a lubrication schedule will ensure maximum performance.
Contamination:
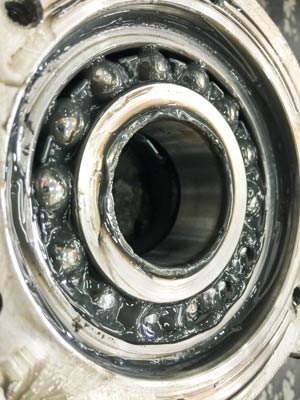
The next common source of bearing failure in spindles is contamination. Contamination can be introduced to bearings through various fluids and particulates, dramatically shortening their life span. Two typical sources of contamination include:
Coolant contamination: Using an air hose to blow coolant and away from your equipment can force various particles into the spindle, contaminating the bearings. Misdirected coolant nozzles can also introduce particles into the bearing. Positive pressure purging seals can be a good line of defense against this form of contamination.
Chip and Air Contamination: Air can be one of the most expensive commodities in a manufacturing plant. In an effort to reduce these costs, machines are often programmed to stop air supply when the spindles are not in process. This is actually a costly mistake. Spindles can operate at very high temperatures, and premature removal of an air hose from a hot spindle can create a vacuum in which contaminates are drawn into the spindle, like solder into a joint.
Chip contamination can also occur when an air hose is disconnected from the spindle and laid into a dirty environment. Turning the air on and letting it run for approximately five seconds before connecting the hose to your spindle is a good method for eliminating contaminants in the air supply.
Mishandling:
While spindles and their bearings may seem like sturdy pieces of equipment, they are actually sensitive to mishandling. Even the smallest impact can set a spindle up for bearing failure. Things to keep in mind when handling a spindle:
Proper storage: Storage of machinery and parts can be different depending on your equipment. When storing spindles, there are a few notable factors that can affect their performance. Maintaining a low-humidity storage area ensures that condensation does not accumulate. Drastic changes in temperature can also affect spindles and bearings. A dry area that does not fluctuate outside of 65°-120° Fahrenheit is ideal for storage.
In addition to stable temperatures, stable levels of vibration are also important when it comes to storing spindles. Spindles should be stored in areas with very low vibration to ensure maximum performance when they are put into use. All coolant and oil ports in a spindle should be plugged to avoid contamination. Wrapping spindles with oil paper also ensures spindle health during storage.
Spindles that have been sitting stationary on a shelf for an extended period of time are also subject to a phenomenon known as micro-welding. After approximately 3-6 months, the balls within the bearing can “weld” themselves to the raceway, which can lead to spindle failure. This can be avoided by hand rotating your spindle periodically by 1-2 revolutions.
Proper handling/installation: Utmost caution should be used when moving a spindle before installation. Even small impacts, burrs, or nicks can reduce performance and lifespan. When it comes time to install a spindle, it is crucial to use the proper tools in a clean work environment. Any form of shock load to the spindle can lead to brinelling, a condition in which the bearing raceways become impacted. It is recommended that installation, storage, and handling all be handled by professionals.
A spindle is the heart of your machine, and bearings could be considered the heart of the spindle. Keeping your spindles in optimal operating condition is crucial in minimizing downtime. By practicing proper methods for lubrication, avoiding contamination, and improving handling, you can ensure that your spindle will operate at maximum efficiency.
About GTI Spindle Technology
At GTI Spindle Technology, we specialize in high quality spindle diagnosis and repair. Getting your business back into full operation and minimizing downtime is our mission. We offer in-house, on-site, and emergency assistance for machine tool spindle failure analysis, spindle repair, and complete spindle testing. With an extensive range and expertise in a diverse group of industries, our customers know that they are getting the highest quality of spindle repair and customer service. Click here to find out more.