In precision manufacturing, machine tool vibration is a critical factor that can significantly impact production quality and equipment longevity. All machinists deal with vibration, or “chatter,” but its complexities often go unnoticed. Let’s look at what it is, its causes, and why it’s crucial to monitor and manage it effectively.
What is It?
Machine tool vibration refers to the oscillatory motion experienced by machine tools, particularly in machining spindles and related equipment. This vibration can occur in various directions and frequencies, potentially affecting the accuracy and quality of the output.
What are the Various Types?
There are three primary types of machine tool vibration as follows:
Free vibrations – sometimes known as random vibrations, these are caused by a shock of some sort — when the tool first contacts the workpiece, when the tool strikes a particularly hard grain in the material, and so on. Free vibrations start at a high frequency and gradually lessen until gone/normalized.
Forced vibrations – which are caused when a time-varying disturbance is applied to a mechanical system. Put more simply, they are caused by forces from either within the machine tool, such as from motors, gears, etc., or from without. Forced vibrations typically exhibit a sudden spike in frequency, followed by a sharp partial drop and then a more gradual lessening until gone/normalized.
Self-excited, or resonance, vibrations – these vibrations occur when a small force — almost exclusively between the tool and chip — cause a small vibration that resonates through the machine and the workpiece, gradually building in frequency until hitting a critical mass. Self-excited vibrations are a common cause of systemic machine failure.
What Causes Machine Tool Vibration?
There are many causes for vibration. A partial list includes:
- Improperly balanced rotating components
- Misalignment of machine elements
- Worn/damaged bearings or other internal spindle components
- Uneven friction
- Gear teeth meshing
- Incompatible materials
- Chip cross section variation
- Loose components
- Insufficient stiffness in tool or workpiece material
- Dynamic loads
- External vibrations transmitted from the environment
- Self-excited vibration caused by trigger forces
Is It Bad?
The quick answer to this question is: yes. At the very least, machine tool vibration can have a negative impact on the quality of your finished parts. If the cutting tool and workpiece are vibrating against each other, cuts will come out rough and uneven or out of tolerance.
Of greater concern and expense, machine tool vibration can cause premature wear to the machine tool itself. Machine tools, and the spindles that drive them, are finely tuned but sensitive equipment. Allowing them to be subjected to vibration over a period of time can and will cause damage, leading to equipment failure and unavoidable repair or replacement.
How Can We Prevent Machine Tool Vibration?
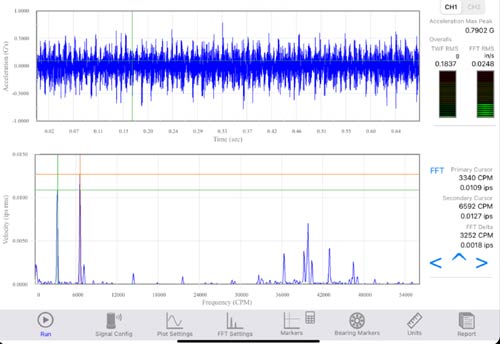
Unfortunately, it is impossible to completely eliminate all unwanted vibration in a real-world environment. However, there are a few ways that you help to lessen them:
- Where possible, isolate equipment such as pumps and motors, from your machine tools
- Reduce the cutting force of the tool
- Change the direction of cutting
- When practical, use tools made with higher-stiffness materials
- Use higher-stiffness workpiece materials
- Ensure your machine tools are properly installed and aligned
- Educate operators on signs of vibration and reporting procedures
Monitoring your spindles and related equipment is key. This can be done manually, or by using predictive maintenance. Consider implementing a vibration monitoring solution, such as VibePro, on your spindles. Solutions such as this can detect unusual vibration patterns early. This allows you to catch and correct problems before they grow into bigger, costlier issues.
Understanding and managing machine tool vibration is essential for maintaining high-quality production, extending equipment life, and avoiding unexpected downtime. By implementing regular monitoring and taking other proactive measures, you can keep operations running smoothly and efficiently.