Anyone that operates high-capacity manufacturing spindles understands that spindle bearing health is critical to the successful operation of a machine. As bearings wear and deteriorate, the performance of the spindle will suffer. If the problem isn’t corrected, then total failure is inevitable. Common causes of bearing failure include poor storage and handling, contamination, overload, incorrect preload, imbalance, and drawbar mechanism failure. Understanding the common causes of bearing failure is essential to counteracting them and extending the life of your spindle.
Bearing Storage
Unused spindles should be kept clean and be rotated periodically to prevent bearings from resting in the same position. When spindles are left to sit for long periods of time the consistent pressure on portions of the bearings can cause flat spots to form. Misshapen bearings are a common cause of spindle failure.
Before mounting a new bearing, check the bearing housing and shaft to make sure they are clean and free from damage. Use the tables supplied by the bearing manufacturer to ensure that the correct amount of clearance will be present when the bearing is installed. When replacing old bearings, make sure you are using new ones that are identical to the manufacturer supplied models, and don’t remove the bearing from its wrapping until it’s time to install.
Contamination
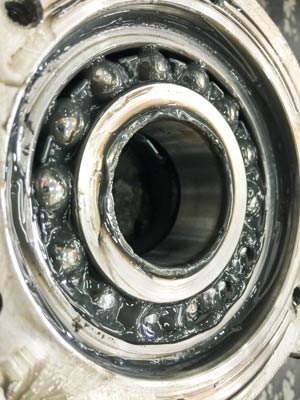
Bearing contamination is one of the most common causes of bearing failure and can be caused by airborne contaminants from compressed air systems, ingress through worn bearing seals, improper or contaminated lubricant, metal debris from internal component failure, and poor installation.
For air-oil lubrication systems, you should only ever use clean, dry, compressed air. Compressor filters should be changed regularly, and an annual compressor air system audit can also help prevent contamination. Seals need to be properly installed to manufacturer specifications to reduce ingress of chips and debris from the machining process. Preventing debris from building up on seals will also extend their usable life as well as reduce bearing contamination.
All spindle, bearing and seal assemblies should be carried out in a cleanroom to prevent contamination, and an expert should be consulted regarding lubrication.
Overload and Preload
Bearing overload can be caused by a variety of external forces, such as feed rate, excessive preload, improperly sized bearings, and improper belt tension. Overloading increases heat which can damage the bearing race.
When a bearing is installed in the spindle, proper preload is vital for good machine performance and to ensure a long bearing life. When the preload is too low, the bearings will skid or skip, whereas excessive preload causes undue friction which leads to excessive heat. Both will lead to poor product quality. Always pay close attention to the operating specifications provided by the machine tool manufacturer.
Imbalance
Imbalance is not only one of the most common problems encountered in high-speed spindles, but it is often the source of many other major problems such as looseness and bearing failure. Imbalance in a spindle can be caused by many influences such as poor drawbar retention, continual pressure on the same points within the tool holder, poor bearing installation, and tool holder or tool imbalance.
Special measuring tools and training are required to detect and correct imbalance. There are industry standard vibration levels to help identify imbalance problems. Imbalance can be corrected in the field with balancing tools and proper training. A best practice for helping prevent imbalance is to require all spindles coming from independent spindle repair companies to arrive with a certificate of balance included.
Drawbar Mechanisms
As the retention force of your machine’s drawbar decreases over time, it will experience chatter, repeatability problems, and degradation of tool life and surface finish. It’s advised that you check the drawbar force at least every two months using a commercially available mechanical gauge. A good time to check drawbar force is whenever you collect your vibration data. You can record and trend drawbar force as a companion to your vibration and temperature levels.
Specified drawbar force will differ with different machines and spindles; be sure you know your manufacturers’ specifications. While a drawbar repair typically costs hundreds of dollars if caught early, drawbar failure can cost thousands when you consider the effects of a spindle crash, spindle grinding, and lost productivity due to downtime.
To get the most out of your spindle bearings, and reduce breakdowns, contact the professionals at GTI Spindle Technology today.
About GTI Spindle Technology
At GTI Spindle Technology, we specialize in high-quality spindle diagnosis and repair. Getting your business back into full operation and minimizing downtime is our mission. We offer in-house, on-site, and emergency assistance for machine tool spindle failure analysis, spindle repair, and complete spindle testing. With an extensive range and expertise in a diverse group of industries, our customers know that they are getting the highest quality of spindle repair and customer service. Click here to find out more.